Thanks to the added capacity of RMS Breaux Machine Works, RMS has enjoyed the added machining capability and expertise to better serve our customers. RMS Breaux Machine Work’s state-of-the-art machine tools and experienced operators have transformed RMS’s in-house machining capabilities and led to improved customer outcomes. Here are some recent examples of work completed across various RMS product lines at the RMS Breaux Machine Works site.
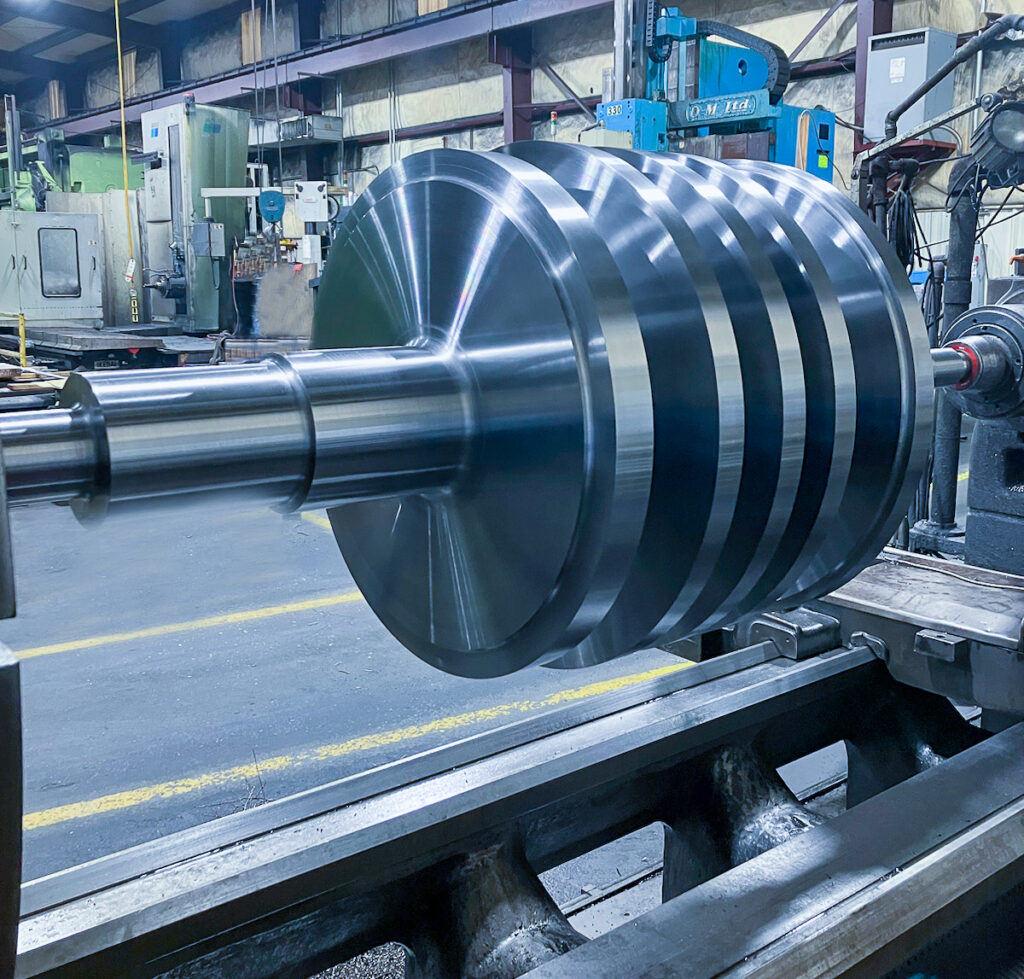
Steam Turbine Machining
This is a new replacement rotor for an Elliott SEPG-5 steam turbine for a refinery customer in Louisiana. It is being machined as an integral rotor meaning that the discs and shaft are made from one forging. Once the machining is complete, the rotor will be ready to have new blading and shaft end components installed by RMS. The steam turbine rotor is on a 50”swing X 204” bed length Ryazan lathe.
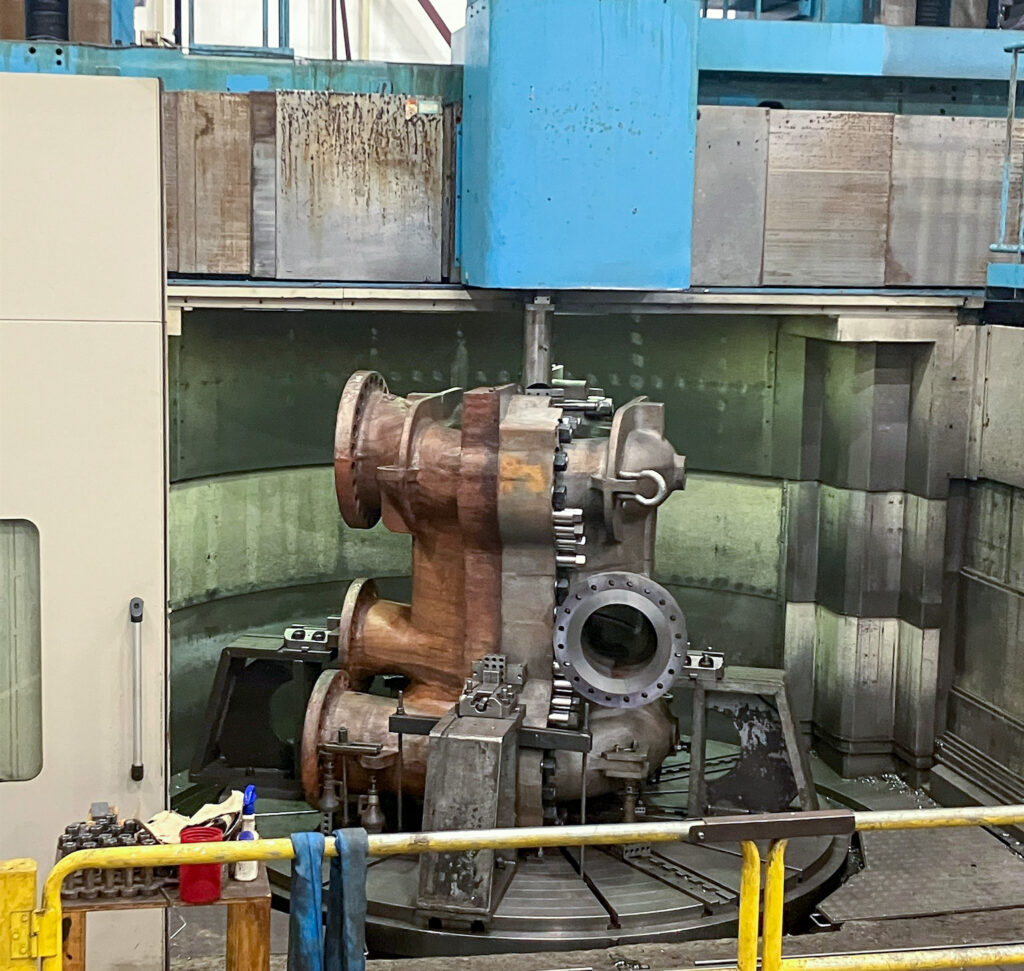
Centrifugal Compressor Casing Machining
RMS is working to overhaul an Elliott 38M centrifugal compressor that has seen over 50 years of chlorine service. RMS Breaux milled the split line which needed to be restored for a precise fit. RMS also line bored the casing to restore concentricity after milling the split line, re-faced all the flange faces and restored all the threaded holes including the vents and drains. This compressor casing is on O-M Neo-30 DX Vertical Turning Lathe with a Center swing of 157” X 138” under rail with a table capacity of 44 tons.
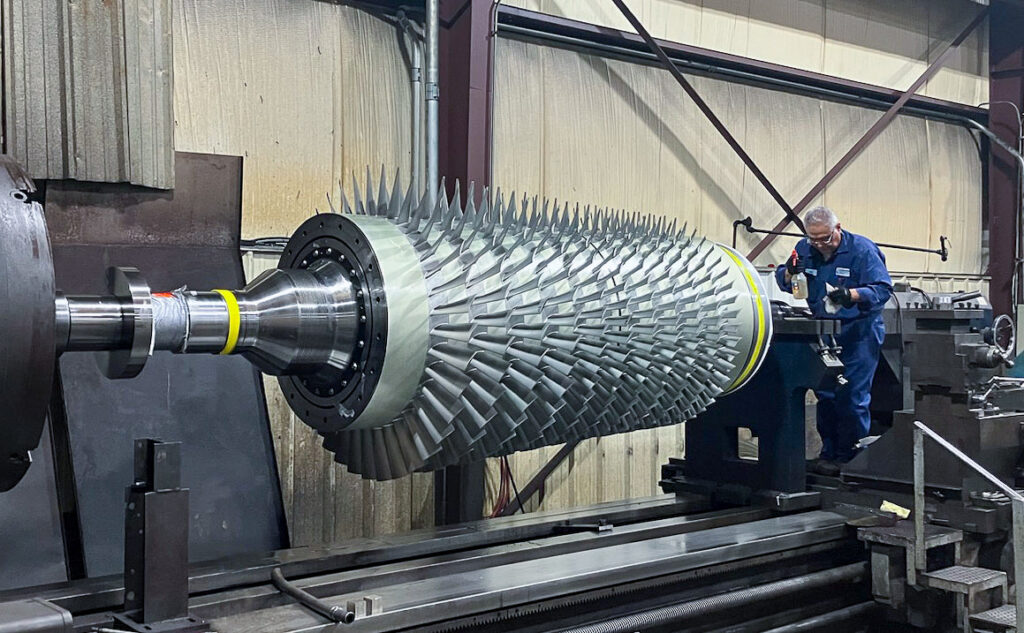
Axial Compressor Machining
This is a new AC Compressor VA-1411 rotor with RMS upgrades for a refining customer. RMS Breaux Machine Works worked to put the finishing touches on and machine the seal strips to their final size. This Axial Compressor is on a 85” swing X 240” bed length Broadbent lathe located at RMS Breaux Machine Works.
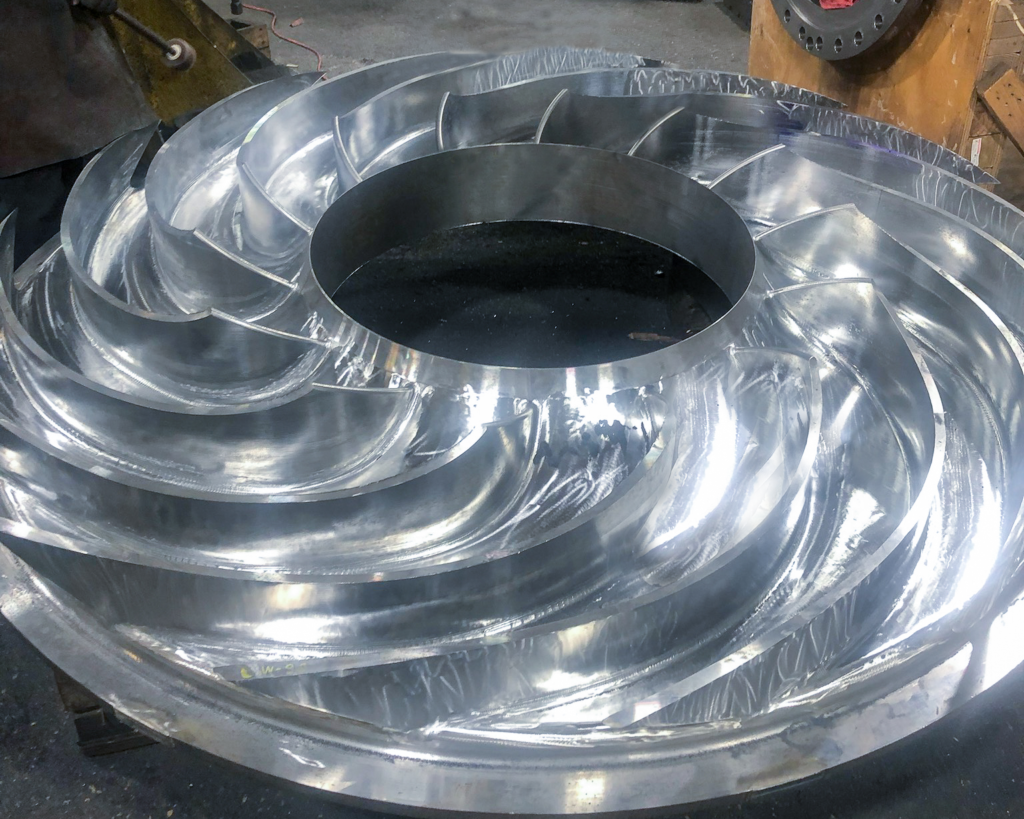
Centrifugal Compressor Impeller Machining
Breaux is working on an impeller pre-machining for a multistage AC Compressor centrifugal compressor. The blades are milled from the hub using a single forging and the impeller cover will be welded to the blades during the fabrication process.
Thanks to RMS’s combination of advanced rotating equipment engineering with a world class machining facility, RMS is able to improve customer outcomes. Bringing these capabilities in-house allows RMS to better serve our customers.