John Korevec, Senior Project Manger • Russ Aerts, Product Director – OFS, Oil Free Screw• Bill Egan, Technical Director – OFS, Engineering
RMS was recently contacted by a Floating, Production, Storage, and Offloading (FPSO) vessel off the coast of Africa for support overhauling their spare 165S4UUA AC Compressor oil-free screw (OFS) compressor. Early in the overhaul of their spare compressor, the OFS compressor in operation unexpectedly shut down, which meant the overhaul of the spare compressor at RMS became a top priority. The shortened turnaround of this 165S4UUA spare required precise coordination by project management, engineering support, expedited supplier timelines, and expedited compressor testing to successfully meet the customer’s new requirements.
Thanks to the diligent work of RMS project management, and the commitment of project stakeholders, the team was able to cut the project lead-time down significantly, thus enabling the expeditious replacement of the compressor on site and minimizing the costly consequences of a unit shutdown on their FPSO.
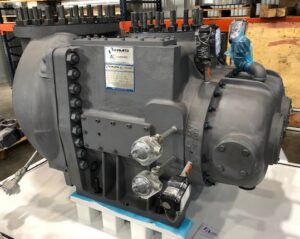
AC Compressor 165S4UUA – Side Profile.
RMS project management worked with RMS’s vendors and in-house OFS experts to repair the 165S4UUA OFS according to the accelerated project plan. The inspection revealed that the unit required repair work on each of the dry gas seals and each of the journal and thrust bearings, as well as new timing gears and a complete cleaning. This required clear, concise and consistent communication by project management to succeed.
The project manager facilitated daily calls and updates with the customer to keep all stakeholders informed on the progress of this project. The OFS Engineering team was also on call to answer any technical questions. After the dry gas seals, bearings and new timing gears arrived, the RMS team immediately got to work on reassembly of this OFS compressor. With guidance and oversight from RMS’s OFS engineering team and project manager, the reassembly was completed within the ambitious timeline.
The 165S4UUA AC Compressor oil free screw compressor was shipped to the Notre Dame Turbomachinery Laboratory (NDTL) where it was set up for its mechanical run test. This mechanical run test also allowed RMS to commission its new dry gas seal panel used at NDTL for all future testing of machines with dry gas seals.
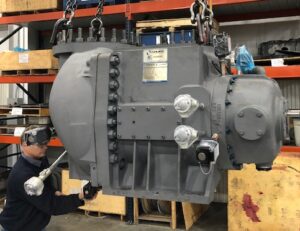
AC Compressor 165S4UUA – Moving
After completing the mechanical run test at the Notre Dame Turbomachinery Laboratory, the overhauled 165S4UUA AC Compressor was air freighted back to the customer in a custom nitrogen purge container provided by RMS.
The RMS Field Services team was on-site at the customer’s FPSO ready to oversee the installation and commissioning of the overhauled AC Compressor 165S4UUA OFS. Before the unit installation, the Field Service team had to meet vaccine requirements, travel visas, and COVID-19 quarantine guidelines.
This expedited overhaul was successful thanks to customer commitment and the engagement of the entire RMS organization that worked together to meet customer requirements and exceed expectations.